A 3D printed component that turns a scuba mask into a reusable N95.
About the Client
Background
Due to COVID, there was a global shortage of personal protective equipment (PPE), especially in the North Texas area. This meant providers were left exposed to the risks of the coronavirus, as front-line workers had to constantly reuse their one-use N95 masks. This significantly increased their risk of catching the virus.
Overview
Dr. Peter Baek, head anesthesiologist at a Tier 1 Trauma Center, and Invene partnered to solve this problem. Together, they developed a 3D printed component that turns a scuba mask into a reusable N95. Dr. Baek provided the clinical experience while Invene provided the technical expertise.
Challenge
This 3D printed component had to adhere to the safety standards set by the CDC. They had to pass the hospital fit test, otherwise, they would not protect the provider from the coronavirus. Hospital administrators had to be convinced of the solution as they were worried about potential liability issues. These 3D printed parts had to be manufactured efficiently as the demand was overwhelming.
3
300
1
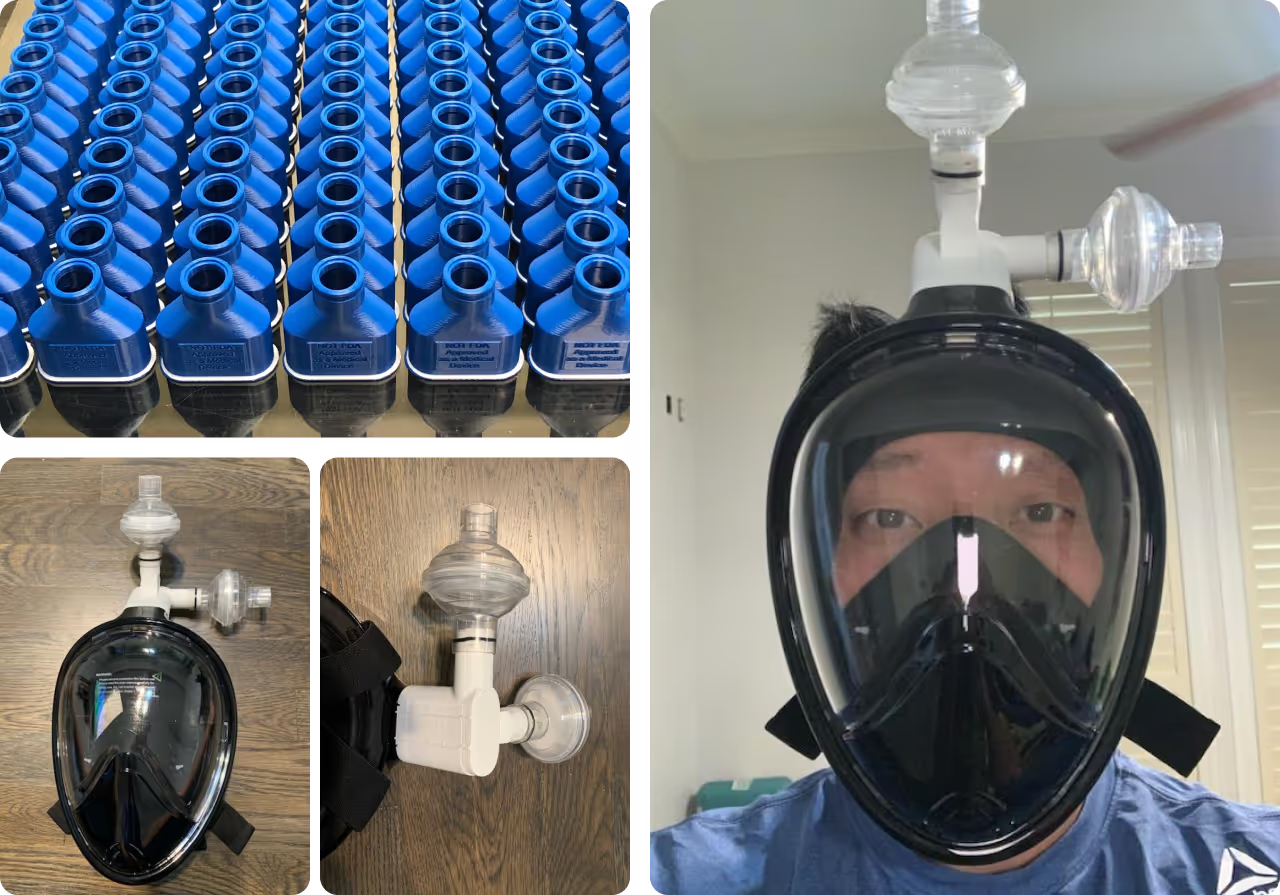
Solution
Invene developed a 3D printed adaptor that cost $4 per part and passed the CDC guidelines. With help from local industry partners like Emerson and the University of Texas at Dallas, Invene was able to quickly manufacture these adaptors. A successful GoFundMe campaign was launched to help cover the costs involved.
Results
Invene distributed over 300 of these adaptors to local doctors in the North Texas area. The result was featured in the Dallas Morning News, D-Magazine, NTX INNO, and various other publications. They also released an open source version (https://grabcad.com/library/texas-adapter-1), to allow others to improve on their design.
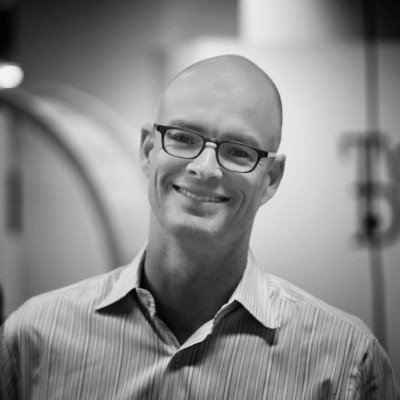
More Case Studies

Can an easy-to-use, direct-to-consumer lab application be built?

Can a physical device be updated without ethernet or WiFi?
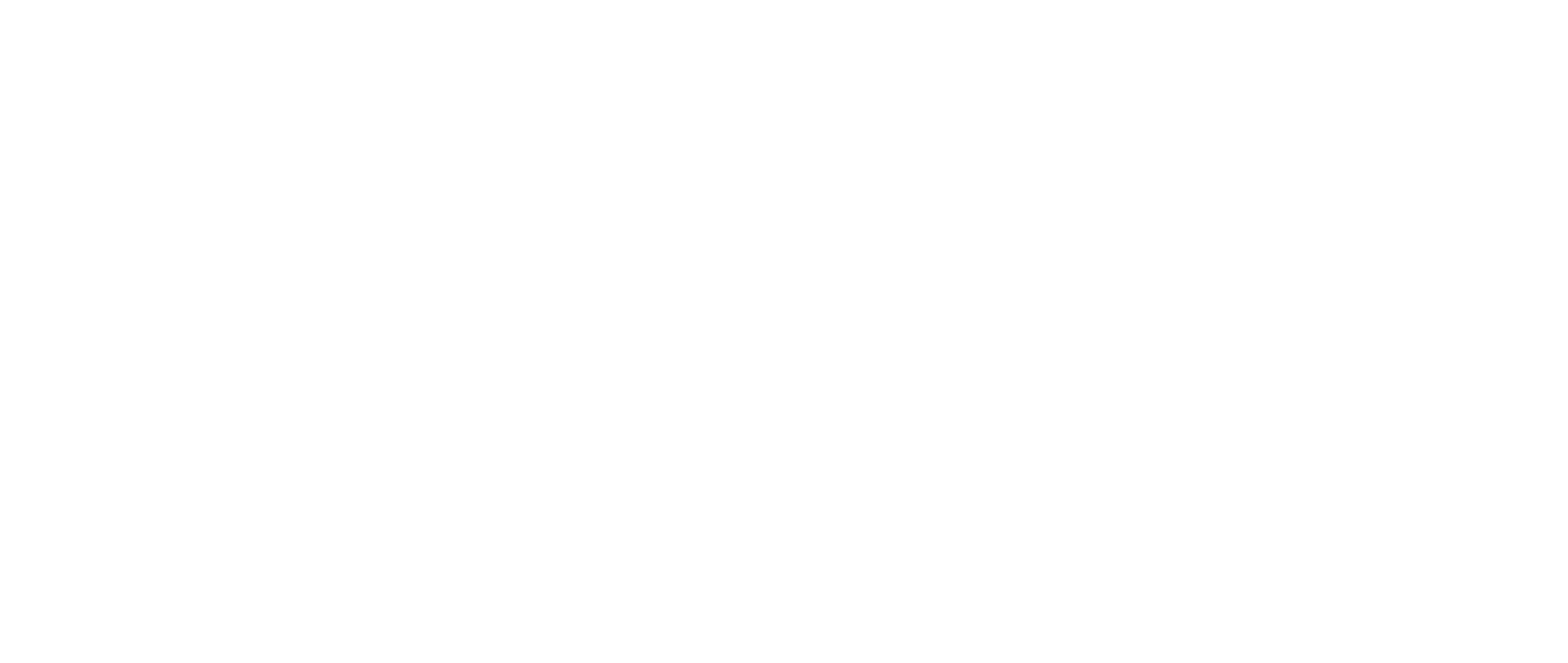
Can concierge healthcare products be delivered efficiently?
Transform Ideas Into Impact
Discover how we bring healthcare innovations to life.